Insights
Advancements in Plastic Injection Molding Market
Thanks to significant advancements and an intensified emphasis on sustainability, the plastic injection molding industry is on the verge of technological upheaval. The sector is projected to grow by 4-5% annually from 2023 to 2028, with this expansion being fuelled primarily by the automotive and packaging industries. The reason for such growth can be attributed to the industry’s capability to produce customized and complex designs, which helps it align perfectly with the evolving demands of modern markets.
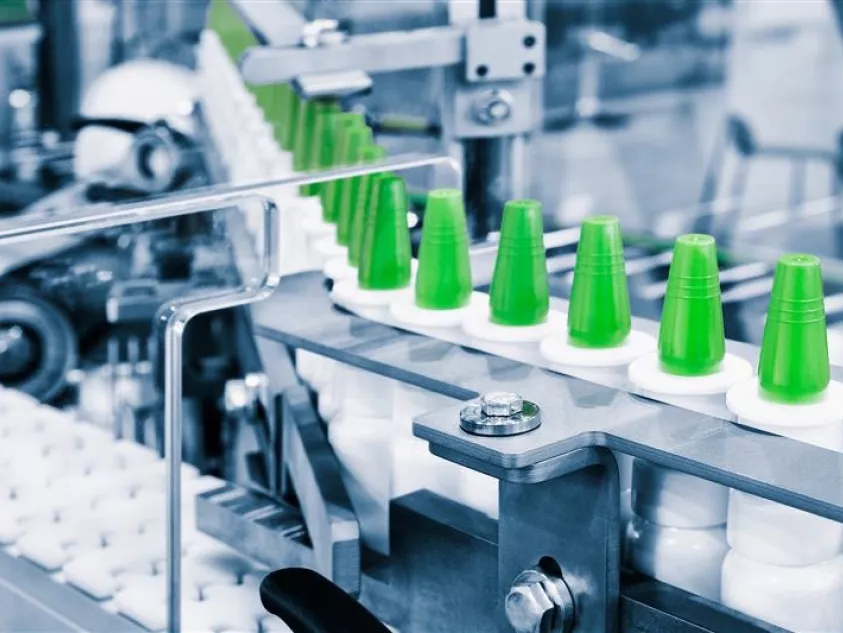
Author- Vignesh V P, Industrial Manufacturing and Durables
Thanks to significant advancements and an intensified emphasis on sustainability, the plastic injection molding industry is on the verge of technological upheaval. The sector is projected to grow by 4-5% annually from 2023 to 2028, with this expansion being fuelled primarily by the automotive and packaging industries. The reason for such growth can be attributed to the industry’s capability to produce customized and complex designs, which helps it align perfectly with the evolving demands of modern markets.
Embracing Sustainability
The industry is actively moving toward using materials that break down easily in the environment, such as bio-PET, polylactic acid, and polyhydroxyalkanoates. These materials are increasingly popular, not just because they are more sustainable, but because of their adaptability. They are useful for a wide range of purposes, spanning from common consumer goods to more niche agricultural tools.
As we see these green materials becoming more widespread, there is a strong initiative to improve their strength and longevity. The future will demand sustainability to be a central part of how we create and think about new products.
Automotive leaders like Toyota, Honda, and BMW, as well as companies like Nestle in the food sector, are incorporating these bio-based materials into their products, which demonstrates their long-term commitment to reducing their environmental footprint.
Advancements in Automation and 3D Printing
The integration of artificial intelligence and Industry 4.0 principles are rapidly changing plastic injection molding through enhanced process monitoring and automated material handling. This increasing automation, including the use of advanced robotics, is making manufacturing processes both more efficient and precise.
3D printing is advancing the production of prototype injection molds, allowing for quicker and more flexible design iterations at reduced costs. This is particularly beneficial for small-scale production where there is a more frequent need for design adaptations to be made.
Micro Molding and Overmolding
Micro molding represents a significant step forward in manufacturing parts with small dimensions, which is crucial for industries requiring high precision like electronics and medical devices. However, creating molds for such minute parts demands extreme accuracy.
Overmolding technology, which merges different materials into a single cohesive unit, has made it easier to create complex, multi-use designs. This step forward has significantly widened the opportunities for innovation in designing new products.
Sustainable Practices in the Industry
In the world of manufacturing, three advancements stand out for their ability to streamline production and promote sustainability:
- Conformal Cooling: This technique optimizes cooling channels to contour product shapes, resulting in reduced cycle times and energy usage.
- Solar Energy: Manufacturing facilities are increasingly using solar panels, which cut costs and reduce carbon footprints, underscoring a commitment to eco-friendly practices.
- Lightweight Plastics: Thin-wall injection molding enables the use of less material while maintaining product quality, enhancing sustainability in high-volume productions like packaging.
These strategies demonstrate the importance of blending technology with eco-friendly measures to boost efficiency and promote environmental care in modern manufacturing.
Industry-Specific Impacts of Innovations in Plastic Injection Molding Market:
Sl. No. | Key Industries | Impact due to advancement factors | Impact Level |
---|---|---|---|
1 | Packaging | OEMs in the packaging industry benefit from sustainable materials like bio-PET, PLA, and PHA, aligning with consumer demand and regulatory requirements. Thin-wall injection molding helps in reducing material costs, while conformal cooling lowers energy consumption and lead time by optimizing cycle times, ensuring quick, cost-effective, and sustainable production. | High |
2 | Automotive | Automotive OEMs see significant gains from automation and bio-based materials. AI-driven monitoring systems enable real-time adjustments to molding parameters, ensuring optimal production conditions. This proactive approach to quality control minimizes downtime and waste, which is essential for the high-volume, high precise production demands of automotive OEMs. 3D printing accelerates prototype mold development, enabling fast design iterations, which are essential for new model introductions. | High |
3 | Medical | OEMs in the medical industry benefit from micro-molding in creating tiny, complex components crucial for medical devices, with overmolding simplifying assembly and enhancing durability. 3D printing offers cost-effective highly customized prototypes with reduced lead time in several medical applications. On the other hand, usage of biomaterials has increased the final prices of molded parts, due to stringent regulatory and quality standard requirements of the industry. | Medium |
4 | Electrical/ Electronics | For electrical/ electronic OEMs, micro molding supports miniaturization for high-precision components, crucial for consumer electronics. Overmolding integrates materials to improve component durability and eliminate the need for assembly, thereby reducing production time in manufacturing parts/ components. | Low |
Case Study: Toyota’s Approach
Toyota has notably integrated sustainability into its design process by using eco-friendly materials in the Prius, which has resulted in a 20% reduction in CO2 emissions. This aligns with a broader strategy to incorporate sustainable resources throughout their production line, steadily raising industry standards. Toyota’s implementation of advanced 3D printing for rapid prototyping not only speeds up production but also cuts costs significantly.
In another transformative move, Toyota’s use of solar energy within its manufacturing facilities has diminished its carbon footprint, reinforcing its commitment to environmentally friendly manufacturing methods.
Toyota's move towards more eco-friendly production is setting them apart as a leader in the field. They are not just thinking about their manufacturing processes but are also inspiring other businesses to consider making similar changes.
The message here is clear, incorporating environmental considerations into how we make things is not just good for our planet, it is a business imperative. It is about shaping an industry that values sustainability as highly as efficiency and profit, guiding others by example towards a more responsible way of operating.
Request a demo
Discover how our solutions can benefit you. Partner with us to unlock potential and drive success. Let's work together to achieve outstanding results.
Get in touch
We’re here to assist you! If you have any questions or need support, don’t hesitate to reach out. Contact us today and we’ll respond promptly to help with your needs.