Insights
The looming sulfur shortage: A hidden risk for global supply chains across industries
Author - Maheswaran Doraiswamy
Senior Analyst - Category Specialization, Chemicals
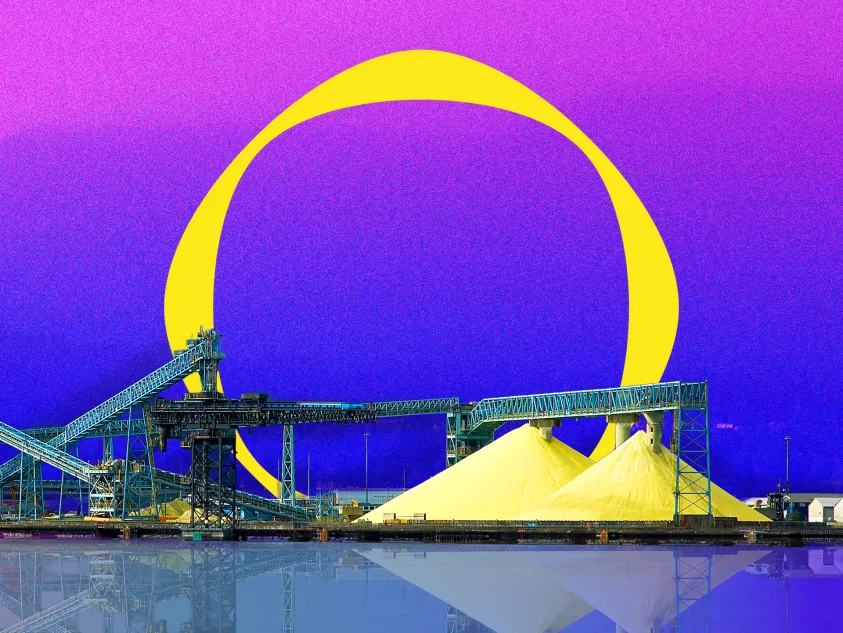
Elemental sulfur, a key component in industrial chemistry, is likely to face a supply crisis that could severely impact multiple major global industries. Over 85% of sulfur is converted into sulfuric acid, vital for applications ranging from fertilizer production to advanced manufacturing. Sulfuric acid’s multifaceted applications, economic efficiency, and pivotal role across critical industries affirm its irreplaceable status in the global market. As decarbonization efforts and declining oil production threaten traditional sulfur sources, a global supply-demand imbalance looms.
This article explores sulfur's pivotal role in agriculture, pharmaceuticals, chemical manufacturing and beyond, while analysing the implications of shifting supply dynamics. Key projections suggest sulfur demand could outpace supply by 2035, with rising prices and industrial pressures as inevitable consequences.
Strategies to address the challenge include leveraging cross-hedging opportunities, diversifying procurement portfolios and Hybrid Procurement Model. The question isn’t whether the shortage will hit—but how industries prepare to face it. Decisions made today will shape the resilience of tomorrow’s supply chains.
Decarbonization and Oil Slowdown
Graph 1 indicates that crude oil production, which accounts for most sulfur recovery, is expected to plateau after 2035, while natural gas production will continue to grow through 2045. However, with investments increasingly shifting toward decarbonization, sulfur supply constraints could emerge since natural gas yields significantly less sulfur than oil.
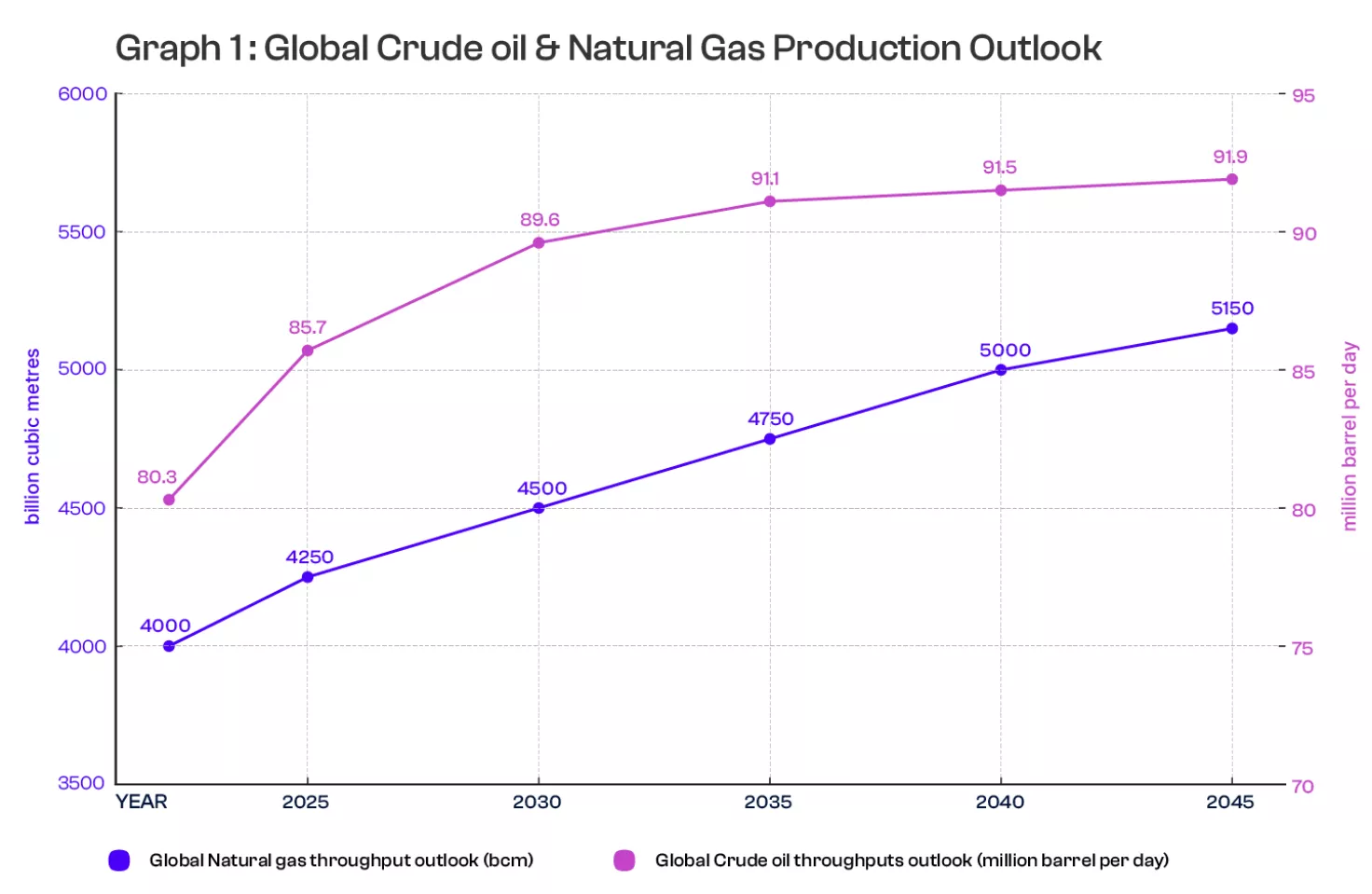
Global crude oil throughout will grow steadily but stabilize after 2035, while regional shifts reshape sulfur recovery. Increasing refining activity in the Middle East and Africa, alongside a post-2030 decline in the US and Europe, will redistribute sulfur supply.
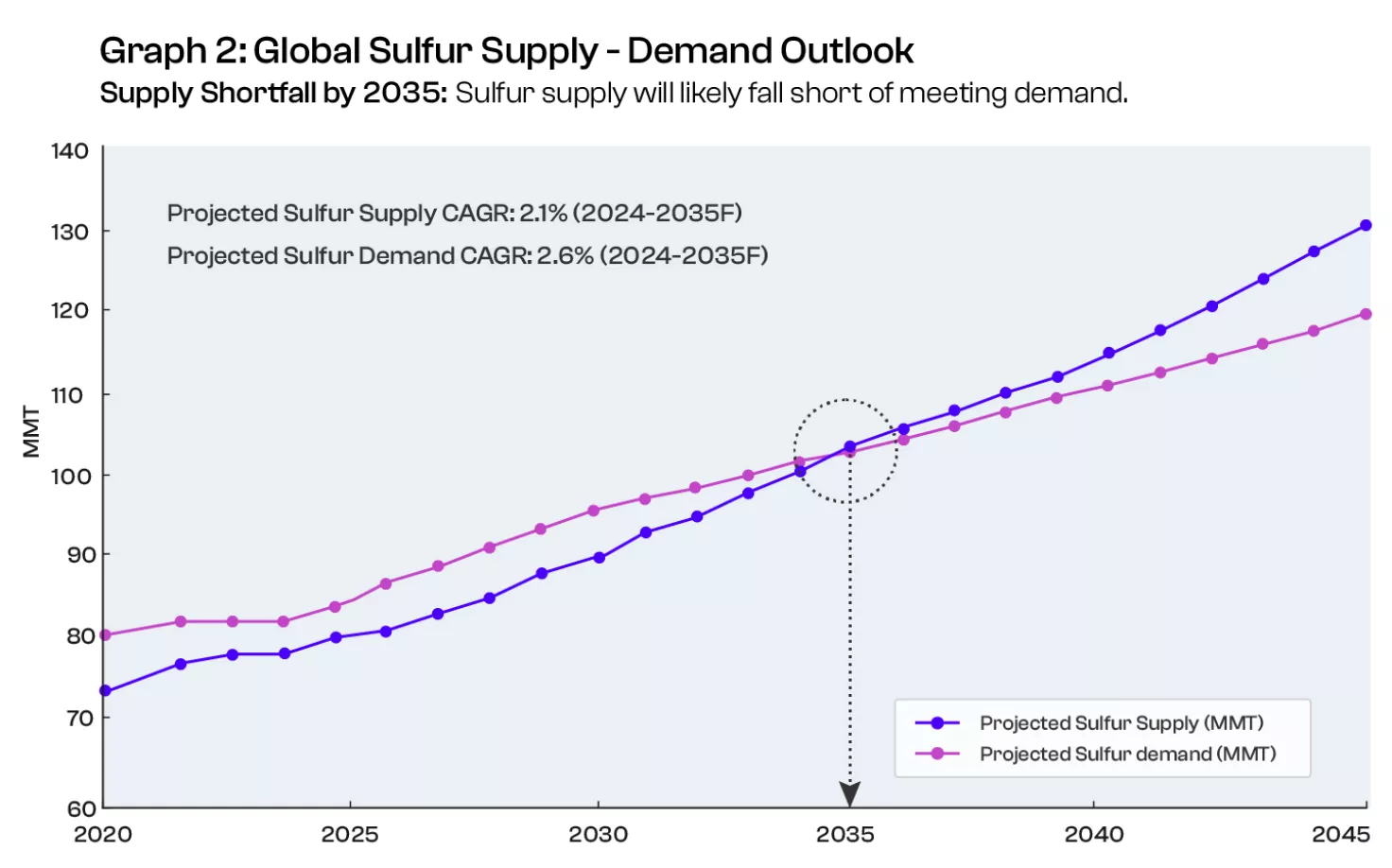
- Base Case Scenario: Assumes equilibrium by 2035, excluding increased sulfur mining due to environmental and cost constraints.
- Optimistic Supply Estimate: Even at 2.1% CAGR, sulfur supply will still be insufficient to meet the projected sulfuric acid demand of 350 MMT.
- Sulfuric Acid Production: Producing 1 MT of 100% sulfuric acid requires 1/3 MT of elemental sulfur.
- Sulfur Required by 2035: To meet 350 MMT sulfuric acid demand, approximately 104-105 MMT of sulfur is needed.
- Supply Deficit: Even with optimistic projections, sulfur availability will fall short, indicating a critical supply gap.
Strategic Insights for Buyers:
- Historical Sulfur Supply Shortages: Sulfur has faced supply shortages before, however, the situation today presents a new challenge. As industries transition from fossil fuel byproduct recovery to direct mining, operating and extraction costs are expected to rise by 40-55%. This shift, while essential, will also result in higher environmental impacts, further complicating supply dynamics.
- Price Volatility and Mitigation: Sulfur price volatility is expected to increase by ~60-75% compared to current levels. However, recycling and alternative sourcing strategies could alleviate 25-30% of projected supply constraints.
- Regional Outlook: Middle Eastern countries (UAE, Saudi Arabia, Qatar) are poised to play a dominant role in the future sulfur market, owing to significant capacity expansions planned for sour gas sulfur plants in the region.
- Reviving Sicily’s Sulfur Mines: Italy’s Sicily, with its untapped sulfur reserves, could serve as a critical lifeline in addressing the impending sulfur shortage. As global solutions struggle to meet rising demand, Sicily’s sulfur mines may become a pivotal backup source—if other avenues fail to meet the growing needs.
Potential Long-term Impact of Sulfur Shortage:
Industry | Impact Level | Impact Detail | Key Insights |
---|---|---|---|
Agriculture | High | Production cost increase of 25-30% for fertilizers. | Major cost increases for essential fertilizer products. Potential impact on crop yields and food prices. |
Rubber | High | Production cost surge of 20-24% due to vulcanization process disruptions. | Increased costs in rubber manufacturing, affecting the automotive and industrial sectors. |
Mining | High | Extraction efficiency decreases of 15-20% with operational cost increases of 18-22%. | Reduced mining efficiency, particularly in sulfuric acid-leaching processes. Cost escalation in extraction. Sulfur is vital for metal extraction, particularly in processes like copper and gold mining, where sulfuric acid is widely used. |
Petrochemicals | High | Manufacturing expense rise of 14-18% with supply chain disruptions affecting 20-25% of production capacity. | Disruptions in petrochemical processes can slow down the production of fuels, plastics, and chemicals. |
Pharmaceuticals | High | Production expense rise of 15-20% for active pharmaceutical ingredient synthesis. | Sulfur is critical for synthesizing key ingredients. Increased costs lead to higher drug prices. |
Water Treatment | High | Operational cost increase of 15-18% with potential treatment capacity reductions of 10-12%. | Increased costs for water purification processes, potential reductions in treatment volume. |
Electronics | Medium | Sulfur-related cost increase of 12-16% for semiconductor manufacturing and metal purification. | Increased production costs in semiconductor and metal industries, potentially affecting tech product prices. |
Pulp and Paper | Medium | Production expense rise of 12-16% with possible quality degradation affecting 8-10% of output. | Increased costs and quality degradation in paper products, affecting brand reputation. |
Cosmetics | Medium | Formula reformulation costs of 12-15% with potential efficacy reductions in 15-18% of products. | Sulfur-based ingredients could compromise product quality. |
Paints and Coatings | Medium | Raw material cost increase of 10-15% with potential supply shortages affecting 15-20% of production. | Increased production costs and potential delays due to sulfur-based raw materials. |
Textiles | Medium | Dyeing process cost increase of 10-14% with colour consistency issues affecting 12-15% of production. | Increased costs and inconsistency in textile production quality. |
Recommendations for Controlling Exposure to Risks:
- Historical Market Correlations: The historical 95% correlation between Middle Eastern sulfur and Chinese sulfuric acid markets presents a unique opportunity for buyers to leverage cross-hedging strategies.
- Emerging Sulfuric Acid Market Dynamics: The oversupply of sulfuric acid in Japan and Korea opens opportunities for a robust "China Plus One" procurement strategy which involves developing diverse sourcing relationships across geographic regions, negotiating flexible agreements with suppliers in Japan and Korea, and building a diversified procurement portfolio to mitigate regional supply chain risks.
- Procurement Contract Strategy: Buyers should prioritize long-term contracts with built-in price adjustment mechanisms. Contracts should also include flexible clauses allowing for volume and pricing negotiations. Developing strong relationships with multiple suppliers will ensure supply continuity.
- Hybrid Procurement Model: Adopt a balanced mix of long-term contracts and spot market purchases, with a pre-agreed cap on price increases.
- Recycling: Implement improved sulfur recycling within the operations, especially in metallurgical or chemical applications where recovery is technically feasible.
Request a demo
Discover how our solutions can benefit you. Partner with us to unlock potential and drive success. Let's work together to achieve outstanding results.
Get in touch
We’re here to assist you! If you have any questions or need support, don’t hesitate to reach out. Contact us today and we’ll respond promptly to help with your needs.